Active Structures Microsystem Laboratory
The Active Structures and Microsystems Laboratory is focused on the mechanics and physics of adaptive materials and their integration into structures and devices. This includes exploring fundamental field-coupled behavior (electric, magnetic, photomechanical, chemical), device and structural dynamics research, and the development of advanced control designs for broadband performance and precision tracking. This requires synergies between materials science, engineering, and mathematics. We collaborate with several researchers that range in backgrounds that include physics, mathematics, experimental fluid dynamics, and materials science to advance the field.
Multi-phyiscs and Multiscale Modeling of Liquid Crystal Elastomers
We are exploring the field-coupled properties of liquid crystal elastomers (LCEs) for integration into a number of adaptive structure applications. These materials exhibit a variety of fascinating properties including photomechanical coupling, shape memory, electrostriction, and chemically induced deformation. Our current work is focused on understanding how liquid crystal domain structures create fast response, large deformation in the presence of polarized light and mechanical loads. Soft elasticity of a nematic phase liquid crystal elastomer is shown in the first image on the right. This monodomain to polydomain transitions that explain soft elastic behavior. The second image illustrates photoelastomer deformation from polarized light. A cubic B-spline plate model was used to obtain high speed computations for nonlinear control applications
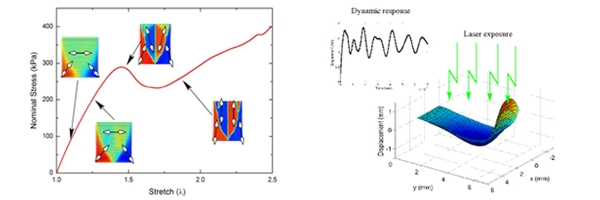
Unifying Model Development of Smart Materials
Material modeling techniques for active materials include a broad number of approaches that are typically focused on predicting a specific field-coupled constitutive relation. Limited work has been conducted on developing a unified theory. Such theories are useful for quantifying underlying field-coupled mechanics concepts to facilitate future materials development and design of adaptive structures. A theoretical approach and computational framework is under development that couples nonlinear continuum mechanics coupled to a set of order parameters that govern field-coupled microstructure evolution and phase changes. Unifying concepts are obtained which illustrate how material constants such as piezoelectric or magnetostrictive coefficients can be predicted without introducing explicit phenomenological parameters as well as nonlinear ferroelectric behavior. An example is shown to the left that illustrates complex soft elasticity in polydomain liquid crystal elastomers under uniaxial loading. In this case, the material model was cross-linked in the isotropic state similar to recent experimental results.
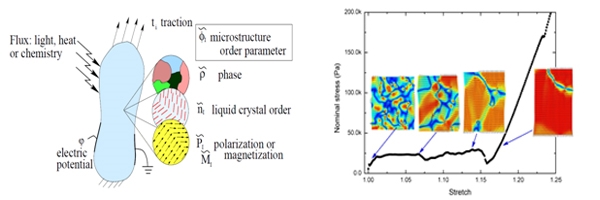
Active Flow Control
Steady flow microjets have shown significant enhancements in mitigating separation flow and reducing noise on a number of aircraft structures including STOVL (short take-off and vertical landing) aircraft, cavity bays, and rotor blades. However, variations in the mass flux is required to achieve a desire performance criteria. Pulsed mass flow injection is believed to enhance flow control; however, broadband actuators that can achieve the necessary momentum for superior control authority are limited. We are currently integrating piezoelectric materials into active microjet systems to understand high speed pulsed microflow. This collaboration, with the Advanced Aero Propulsion Laboratory (Dr. Farrukh Alvi), is focused on synergies between experimental fluid dynamics and next generation smart structures for aerospace applications. Two example is shown here. The first actuator, a piezohydraulic system, is used for fundamental pulsed flow characterization from quasi-static up to ~800 Hz. The second actuator eliminates hydraulic fluid by using an activel deforming converging-diverging nozzle that is control by a piezoelectric actuation.
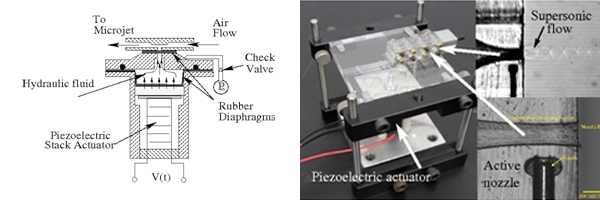